Improved paint durability on Boeing commercial airplanes.
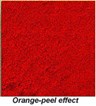
The use of exterior decorative paint on Boeing airplanes is very important to operators because it projects their corporate image and differentiates them from other operators. As a result, overall appearance and durability are critical requirements of any exterior paint. In 1998, Boeing paint hangars in the Puget Sound region switched from conventional paint systems to high-solids primers and topcoats. The company made the changes to improve the color and gloss durability of the topcoat paint and to meet new regulations that mandated the use of primers and topcoats with low volatile organic compound (VOC) content. These regulations also required Boeing to use new, less aggressive cleaning solvents before applying paint. Using new solvents, paints, and application processes produced several challenges in preparing the surface, painting, and achieving a finished appearance satisfactory to operators. Since the regulations became effective in late 1998, Boeing has gained related experience and knowledge about the following:
Physical properties of high-solids paint
Qualification of high-solids paint
Surface preparation and painting of airplane skin
Operator in-service data on performance of high-solids paint
Follow-up activities required by Boeing
Physical properties of high-solids paint
The U.S. Environmental Protection Agency issued new requirements for the use of primers and topcoats with low VOC content effective September 1998. These requirements, called the National Emissions Standards for Hazardous Air Pollutants (NESHAP), reduced the VOC content of primers to 350 g/L from 650 g/L and the VOC content of topcoats to 420 g/L from 600 g/L. The reduction in the amount and type of solvents used in high-solids primer and topcoat created a challenge for both suppliers and users in developing and qualifying acceptable paints. These new paints must meet all engineering performance and application requirements and provide a finished appearance that is acceptable to operators. The performance and application requirements of solvents in high-solids paint are divided into two categories: wet film properties and dry film properties. Both these properties have changed for the primer and the topcoat.
Wet film properties. Conventional paint (both primer and topcoat) uses large volumes of solvent to keep high-molecular-weight, long-chain hydrocarbon polymers in solution (in a liquid state). This gives the paint a longer application life and makes it easier to apply.
High-solids paint generally contains low-molecular-weight, short-chain polymers to allow for a greater solids density and lower solvent content. As a result, the paint maintains its required flow characteristics while meeting NESHAP requirements for reduced VOC content. The combination of low VOC and high-solids content enables the paint to cross-link more densely. High-solids paint forms many more chemical bonds between resin chains than does conventional paint, making it more stable. Cross-linking affects paint properties such as chemical resistance and flexibility. The flow characteristics of the paint, also called rheology, are controlled with a blend of solvents and additives. The short-chain polymers are viscous liquids that continue to flow after spraying and after all the solvent has evaporated. Controlling the rheology of the paint is critical to producing an acceptable appearance. If the paint viscosity is too low during and after application, the paint will run and sag. Conversely, if the viscosity is too high, the paint does not flow well and the result is a bumpy "orange peel" appearance.

Dry film properties. The dry film properties of a paint determine how durable the paint will be in service. These properties include corrosion resistance, color and gloss stability, chemical resistance and flexibility, and adhesion. Boeing evaluates candidate paints for these properties using Boeing Material Specification (BMS) 10-72 for exterior paint. The specification qualifies primer and topcoat systems from the same manufacturer that have been developed to perform best when used together.
Exterior primers provide primary corrosion protection to the airplane exterior. Protecting airplanes against corrosion is critical to structural safety, and this protection affects the service life of the airplane. Exterior primers contain hexavalent chrome, which is the most effective corrosion inhibitor available for aluminum. This inhibitor must protect primary structure in inaccessible areas, such as fastened joints, for the designed service life of the airplane.
Topcoats provide the decorative paint scheme for airplanes. Ultraviolet (UV) light degrades certain pigments and resin systems over time. In an acidic environment, such as a volcanic eruption or severe air pollution, color shift occurs (the paint changes color, usually growing darker and less brilliant), and topcoat gloss decreases. Boeing evaluates paint for color and gloss stability using the UV/acid weathering test, which was developed to simulate the types of color and gloss degradation noted during the eruption of Mt. Pinatubo in 1991. Results from the UV/acid evaluation of BMS 10-72 Type VIII and Type IX paint topcoats showed that both these topcoats provided significantly more color and gloss stability in an acidic environment than conventional topcoats.
Primers and topcoats also must perform together as a paint system. These systems must be resistant to chemical attack because airplanes are often exposed to hydraulic fluid, fuel, and maintenance chemicals when in service. High-density polymer cross-linking provides the required chemical resistance in high-solids paint, but cross-linking also affects the flexibility of the paint. Flexibility and adhesion of paint systems are crucial because of the thermocycling, aerodynamic forces, and body structure stresses put on the airplane between takeoff and landing. Paint manufacturers must balance chemical resistance and flexibility with cross-link density in high-solids paint. They also must ensure that the paint system meet the adhesion requirements in BMS 10-72.
Return to Table of Contents
Qualification of high-solids paint
In the past, Boeing switched between different conventional paint systems to take advantage of improvements in dry film properties. Because these improvements were made within the conventional paint formulation technology, any resulting changes in application were minor for the painters. However, when Boeing began using high-solids paint, it quickly became obvious that the initial high-solids paint formulations affected paint application properties and needed to be improved. Identifying these issues required rigorous laboratory and incremental scale-up testing.
Laboratory testing. The greatest variety of paint applications and cure conditions can be replicated in laboratory testing. Small panels of airplane skin materials are painted to investigate the mechanical and chemical resistance properties of a paint. These properties range from color stability to hydraulic-fluid resistance to adhesion. Application tests define how environmental parameters, temperature, and humidity affect the cure kinetics of a paint (how a paint cures or hardens). This stage of testing is designed to define such application parameters as the dry-to-tape time of a paint, which is the time that elapses between paint application and the point when masking tape can be applied without leaving a mark.
Tests also are performed to identify potential appearance defects such as solvent pop and microblistering. Solvent pop occurs when the outside of a paint film cures or hardens before the solvent diffuses from the paint film. The solvent continues to leave the paint but has to break through the hardened paint surface to do so. As a result, small pot marks form in the paint surface. Microblistering is similar to solvent pop, but instead of solvent, carbon dioxide gas from the polyurethane cure reaction breaks through the paint film and leaves marks on the paint.
Scale-up testing. After laboratory testing with small panels, scale-up testing continues with large panels, progresses to test tubes sprayed by production personnel, and finishes with production trial airplanes. Large panels of airplane skins are tested mainly to discover appearance issues such as defining the wet edge time of a paint or how long a new coat of paint will blend into a previously applied paint. If a paint has a short wet edge time, the airplane will look striped. The stripes will occur where the paint stacker positions meet. Short wet edge time also will prevent overspray from blending into the paint film, resulting in a rough surface.
Another result noted in large-panel testing is paint-gun effects. Different paint guns can break up the paint differently and can affect both the appearance of the paint and contamination sensitivity of the primer. The paint hangar's electrostatic guns do not atomize the paint as finely as high-volume/low-pressure (HVLP) paint guns. The electrostatic guns produce larger paint droplets that lose less solvent during spraying than with HVLP guns. As a result, the paint film from electrostatic guns flows more easily and produces a smoother finish. However, a surface energy defect on the substrate, such as silicon residue from window and door seals, can cause the paint or primer to flow away from the defect, preventing a smooth, continuous film and leaving the appearance of fish eyes or slug tracks on the paint (dewetting).
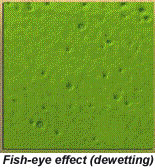
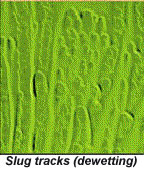
Spraying test tubes (nonproduction airplane sections) verifies the laboratory testing under factory production conditions such as paint stacker movement, factory airflow production painter, and production cure conditions. Defects seen in this phase of testing include the effects that look like tiger-striping (in gray paint) and seeding. Tiger-striping results from uneven paint pigment mobility. In the case of gray paint, the small, fast-moving black pigments move to the edge of freshly applied paint while the large, slow-moving white pigments stay in the center of the film, producing a striped appearance. Seeding results when paint pigments clump together, giving the paint film a sandy or gritty appearance. The root cause is pigment dispersants, which are less stable and more sensitive in high-solids paint than in conventional paint.
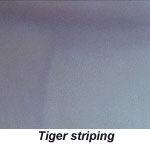
Production trials are the final verification that a product is ready for implementation. Although scale-up tests precede them, production trials have produced additional paint defect issues that must be corrected. These include wrinkling in topcoat paint that occurs when the paint layer forms a cured film while the inner layer stays liquid. The wrinkling was attributed to strong solvents that reacted with the paint can; the longer the paint sat in the can, the worse the condition became. Another defect was dewetting. Because the primer was uneven and bare metal often appeared where the primer pulled back, the finish looked poor and the primer adhesion properties were suspect. Dewetting was caused by the way the new primers interacted with the various and complex materials used on the airplane.
Return to Table of Contents
Surface preparation and painting of airplane skin
The NESHAP regulations required Boeing to change all components of the paint systems (solvent, primer, topcoat, and application techniques). They also specified that any cleaning solvents used before painting must have a vapor pressure below 45 mm Hg. As a result, in conjunction with the new high-solids primers and topcoats required, Boeing began using NESHAP-compliant solvents that are less aggressive than the solvents used with conventional paint systems (such as blends of methyl ethyl ketone [MEK] and toluene).
Surface preparation for painting begins with using an alkaline cleaner to remove the green temporary protective coating from the airplane skin. The airplane then is wiped with solvent and abraded. To meet NESHAP regulations, Boeing switched from the fast, strong, and effective 100 percent MEK solvent to a slower evaporating solvent blend of methyl propyl ketone and MEK.
Boeing also found an alternative to abrading in the form of a recently developed acid cleaner called Chemidize.
Water then is sprayed over the airplane surface to clean it. Premature breaks in the water film are a result of contamination. This is similar to the sheeting action of water on a clean glass. Breaks in the water indicate that the glass is dirty.
After the surface is free of water breaks, the airplane is ready for the three-step finish system: conversion coating, primer, and topcoat. The chromated conversion coating, alodine 1000, allows the primer to adhere to the oxide that is created on the airplane skin during conversion. Adhesion occurs when the alodine reacts with the aluminum oxide and converts it into a mixed chromate-aluminum oxide, which provides good adhesion for the primer. After the excess alodine is rinsed off and the airplane is dried, it is ready for primer and topcoat.
Primer is applied to adhere to both the oxide and the topcoat to protect the aluminum skin from corrosion. It is applied in one coat, typically 0.5 to 1.0 mil thick, and must cure in 2.5 hours. After curing, masking tape is applied to define the decorative paint scheme for the airplane.
Three spray passes of topcoat then are applied to achieve a coating 3 to 5 mils thick. The paint hangar then is heated to accelerate the curing process. The taping, painting, and curing processes may be repeated several times to finish the paint scheme.
Return to Table of Contents
Operator in-service data on performance of high-solids paint
Beginning in 1999, Boeing collected service data on selected airplanes with the Boeing-qualified high-solids paint. On some of these airplanes, the surface was prepared using Chemidize instead of power abrading. Operator complaints focused on paint adhesion in general and paint erosion in specific areas such as wing leading edges and radomes.
The limited surveys did not reveal any color and gloss degradation of the topcoats, which the UV/acid test showed were more durable in an acidic environment. However, Boeing received reports of color or gloss degradation on paints that the UV/acid test suggested would not be as durable in an acidic environment. Paint adhesion problems also were noted during the limited survey. Most of these problems occurred at the same location on a specific model where the paint peeled (lap splices, rivets, and fasteners).
Boeing identified one possible cause for the paint failures as the sensitivity of high-solids primers to contamination. Conventional paints are more tolerant of contamination because the large quantities of solvents they contain help dissolve and distribute the contamination. This reduces the probability of a critical concentration buildup of contamination that might lead to paint failures.
In addition, the less effective, slower evaporating handwiped solvents now used during the cleaning process do not remove contamination as effectively as more aggressive solvents with higher vapor pressures. Power abrading removes the oxide layer from the airplane surface for better alodine adhesion and removes any residual material, such as sealant, that could also affect adhesion. However, power abrading areas near lap splice or butt join can be difficult. Boeing continues to evaluate new cleaning processes to more uniformly clean areas that are difficult to reach.
Boeing also investigated the possibility that fastener-head finish or the installation process for fasteners and rivets may have caused paint adhesion failure on these parts. Some corrective changes have been implemented as a result, but they have not been identified as the comprehensive solution for this particular adhesion problem.
Return to Table of Contents
Follow-up activities required by Boeing
Boeing is making some near-term changes to improve the robustness of the high-solids paint it uses, including slight formula changes to eliminate some special handling requirements and potential appearance defects. The company also is developing and measuring techniques to improve paint consistency and application reliability, rheology, and paint flow measurements. A consistent paint vendor product will yield higher quality airplane paint, and Boeing continues to pursue the qualification of paint systems, primer, and topcoat from a single vendor.
Long-range activities will include improving the durability and appearance properties of currently used paints as well as the number of appearance options available. For example, Boeing is targeting the orange-peel appearance noticed in some finishes. Improvements in paint rheology and a better understanding of application parameters (such as paint-gun type and setup) and measurement devices should result in an improved surface. Using new polymer types may improve paint durability, and experience gained with the new high-solids paint will help Boeing efficiently evaluate any new paint.
Boeing also is investigating further the paint adhesion problem related to fasteners and rivets. Eliminating this problem will involve better understanding the relationship between the stresses encountered on the fasteners and rivets, environmental factors, and the mechanical properties of high-solids paint.
Return to Table of Contents
Reprinted from AERO magazine by permission of The Boeing Company.