Gas Turbine And Aerospace Component Manufacturer Upgrades CMM Measuring Capability With Two New Wenzel Bridge-Type CMMS
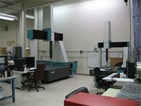
Danville Metal Stamping Company was founded in 1946 as a manufacturer of basic stamped parts. Since that time, the company has successfully built a reputation as a high-quality fabricator with extensive know-how and experience as a producer of sophisticated gas turbine and aerospace components. The company employs approximately 450 people involved in forming and hydroforming, CNC and laser machining, and joining technologies, as well as added capabilities in welding, heat treating and vacuum brazing.
Scott Bean, Danville's lead CMM programmer explains, "Our CMM measuring is a vital part of our manufacturing process, and as the complexity and size of the components we produce have increased, we recognized the need for a larger CMM machine with a high degree of accuracy to replace the Brown & Sharpe Xcel UHA that we had been using with ongoing accuracy and repeatability issues. We were also beginning to become frustrated by issues with the PCDMIS software and both were beginning to negatively effect production and delivery schedules. For many years Danville had been a Beta test site for PCDMIS but we now felt is was time to expand our capability, and we began to survey what was available in new equipment as well as new software. When we attended the Quality Show in 2007 we discovered Xspect Solutions, their
OpenDMISsoftware and the new Wenzel CMMs that they sell and service. The ruggedness, inherent accuracy and variety of features of the Wenzel CMMs were ideal for the level of measurement we require for our aerospace components. Their OpenDMIS software as was exactly the kind of product we were looking for there, as well. One that seamlessly integrates CAD data with the CMM programming and measurement process, providing us with the high level of power, precision and productivity with just a single click. The software has easy drag-and-drop features from the database area into the adjacent programming window that automatically generates the underlying DMIS 5.0 code together with probe and alignment definitions. The kind of complex CMM programs that we work with can be created in a few minutes and simulated, utilizing the powerful simulation and collision avoidance tools standard in OpenDMIS. We have already realized a 20 percent savings in programming time as compared to PcDMIS."
"We scheduled a visit to the Xspect Solutions/Wenzel facility in Wixom, Michigan and ultimately came away with two new Wenzel machines both equipped with OpenDMIS software," Bean says. "One machine was a large Wenzel LH 15.20.12 bridge-type machine with a measuring envelope of 1500 x 2000 x 1200 mm, and a smaller LH-8.10.7 with a measuring range of 800 x 1000 x 700mm. Each machine has a maximum 3D measuring speed of 700 mm/sec with maximum acceleration of 2,000mm/sec2. They are equipped with a Renishaw TP20 probing systems and we added the HT400RC wireless teach pedants because it eliminates the tedious keyboard interaction necessary with conventional CMM teach pendants. Our ultimate desire is to add scanning probes to these machines to speed up the measuring process for many of the airfoil components we produce." Bean adds, "Because Xspect Solutions was able to take our existing CMM machine in trade, we were able to purchase both machines for what we typically would have paid for just one machine. In addition, we have been very pleased with the training program that Xspect Solutions offers. To date we have had two of our four measuring technicians trained on OpenDMIS and our other two will soon follow."
SOURCE: Xspect Solutions, Inc.